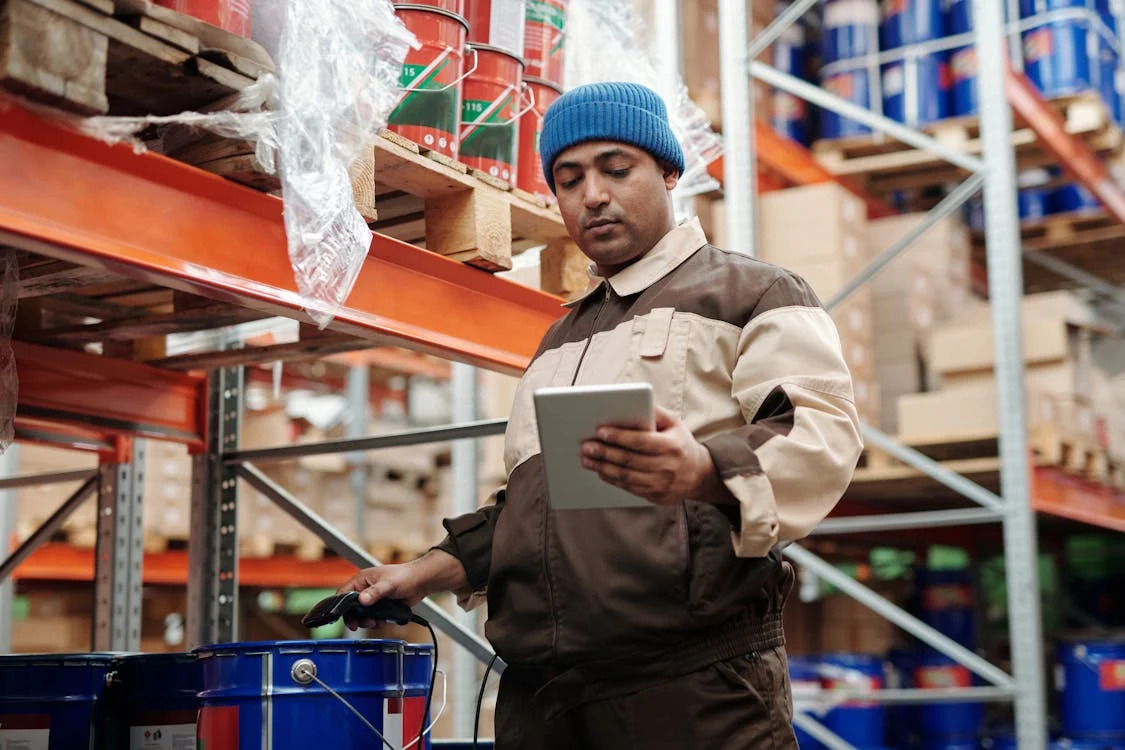
Every storage facility needs to focus on rack safety since damaged racks will result in dangerous situations alongside damaged products and operational delays. Running a rack safety audit allows you to verify the stability of your storage system while ensuring all regulations and minimising accidents. This guide demonstrates how you would conduct an extensive inspection of warehouse racks by following an organised process.
1. Establish Audit Objectives and Scope
Before beginning the audit process, clear objectives and a detailed scope definition should exist. The audit scope needs to establish how many racks within the warehouse will be examined and whether it focuses on certain areas. Different aspects, including structural stability, maximum weight limits, and danger areas, need clear examination expectations.
The planning phase should include stakeholders who represent warehouse management and safety personnel. A joint effort between stakeholders ensures the audit examines serious safety issues while following organisational guidelines and external regulations. The process will create an initial conditions assessment, which can support ongoing rack inspection protocols.
2. Perform a Visual Inspection
You should now carry out a visual assessment of the racks. Check for visible indicators of damage, such as bent beams, broken welds, or signs of wear on the structures. Look for overall system wear by inspecting the pallet rack system to identify any excessive damage that might affect its stability. Check for safety hazards, such as debris or clutter, that might block the racks from being properly used.
Check the instalments of the racks to determine their overall performance. Assess all anchor points for stability, then confirm the racks maintain both levels along with appropriate alignment with nearby structures. Racks become unstable when they lean or have faulty installation methods. Safety labels, weight limits, and load signage need to be present and readable according to visual inspection requirements.
3. Check Rack Load Capacities
Every rack has limitations regarding weight capacity, so the threshold should be checked before placing any objects on it. A rack overloaded with weight endangers its structure, leading to possible incidents and injuries. Check the manufacturer’s load capacity values against weight measurements for stored goods, including pallets or shelving units.
Procedures need to be executed immediately after discrepancies, such as excess weight are found during the audit process. Warehousing personnel should consider multiple ways to manage weight distribution to prevent rack damage while improving storage equipment. Warehouse safety remains secure when regular audits detect excessive weights and verify that weight limits stay within specifications, minimising accidents and warehouse safety risks.
4. Inspect Rack Accessories and Components
Users must inspect all accessories in addition to the racks to ensure proper functioning. The rack accessory evaluation should include safety bars, wire mesh, pallet supports, and end protectors. Examine the racks for evidence of both structural damages and material wear conditions that might affect their technical capability. An inadequate maintenance programme of accessories results in structural weakness, raising the risk of accidents.
Check that all components have proper installation and meet safety requirements. Monitor safety devices for proper functionality to prevent falling objects and stand to utilise the structure. The safety of your material handling and storage system will increase when you perform regular cheques and proper maintenance on these accessories.
5. Review Compliance and Maintenance Records
Completing the audit process requires examining maintenance and compliance records linked to the racks. The auditor verifies whether inspections and maintenance activities occurred according to company and regulatory standards. Previous audit results need to be assessed to confirm the implementation of proper corrective actions.
Look for documentation about rack maintenance history and records of repairs and upgrades. Guarantee that the warehouse area satisfies OSHA and local industry regulations’ safety requirements. Records about rack conditions help identify safety challenges over time so that distribution centres and warehouse operations can receive swift solutions.
Final Thoughts
Organisations must conduct rack safety audits to create safe warehouses with optimal efficiency. These five approved steps can help you recognise possible risks while implementing proactive measures to maintain workplace safety conditions. Rack safety audits prevent workplace incidents, increase storage system durability, decrease operational disruptions, and ensure standard warehouse safety compliance.At Rack Safety Singapore, we stand ready to assist businesses that want to enhance warehouse safety and operational efficiency. We are specialised experts who conduct thorough rack audits, perform maintenance services and issue certifications to help your facility meet all mandated regulations. Call our team now to set up an appointment for better warehouse safety for your premises.