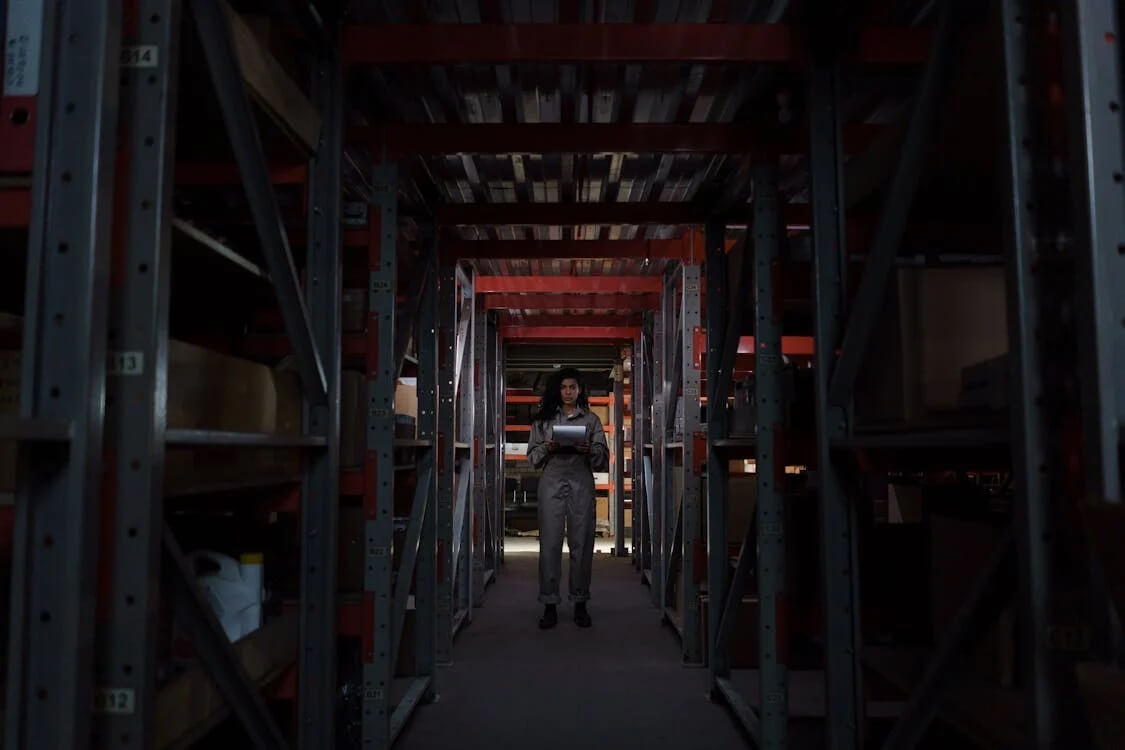
Rack inspection is crucial for workplace safety and friendly warehouse operations. Safety inspections of pallet rack systems enable businesses to spot conceivable dangers, avoid accidents, and guarantee regulations. In this guide, we will outline five essential steps on how racking inspector can conduct thorough assessments that protect personnel and assets.
1. Visual Assessment and Documentation
Before starting a detailed decoration of the entire warehouse racking system, the inspector must first make a full visual assessment of the racking warehouse system as a whole. Then, the inspector must visit the facility and write down every bit of wear and tear the facility undergoes, such as bent uprights, broken components, or lost safety pins. Then, the inspector must map out the storage equipment, document the layout to practice, and follow a systematic inspection so that nothing is missed.
This first phase relies heavily on photo documentation and visual checking through rigorous scanning. If your rack installation is old, take clear pictures of the rack’s current state to note where you can see signs of deterioration. These photos will be great reference points for future assessments and measure how much damage has progressed over time.
2. Structural Component Examination
Examine each structural component of the rack system in detail, starting with the uprights and moving on to the beam connections and bracing. Check for signs of corrosion, deformation, or fatigue in the metal components. Pay particular attention to areas where beams connect to uprights, as these junction points often experience the most stress.
Measure any deflections or deviations from vertical and horizontal alignments using appropriate tools. Compare these measurements against the manufacturer’s specifications and rack safety standards. Even small deviations can indicate potential structural issues that could compromise the entire system’s integrity.
3. Load Assessment and Capacity Verification
Review and compare the current loading conditions with the manufacturer’s rated capacity. Check that load indicators and safety signs are visible and accurately reflect the maximum allowable weight for each beam level. Verify that the actual stored weights do not overload these limits.
Inspect pallets and storage units to ensure they are properly positioned and do not cause deflection stress on the structure. Look for signs of excessive loading, such as sagging supports or buckling uprights. Document any instances where load limits are being approached or exceeded.
4. Risk Assessment and Safety Feature Verification
Conduct a thorough risk assessment of all safety features, including row end barriers, column guards, and pedestrian safety barriers. Ensure these protective elements are properly installed and in good condition. Check that all safety locks and pins are in place and functioning correctly to prevent component disconnection.
Review the placement and condition of load notices, safety signs, and operational guidance materials. Verify that all required safety markings are visible and legible. Document and schedule any damaged or missing safety features for immediate replacement.
Final Thoughts
Using a systematic inspection method for racks is vital to maintaining an orderly and temperate condition in a warehouse. By following these five steps, with good file keeping, organisations can greatly decrease the likelihood of incidents and adherence to safety regulations. Properly regular inspection and quick response to indicated harms will assist in extending the system’s lifetime and safeguarding sensitive assets and personnel.
If you want to ensure the safety and longevity of warehouse operations, Rack Safety Singapore carries out comprehensive solutions. We specialise in comprehensive rack inspection services, safety solutions, or expert guidance on keeping your systems compliant and secure. Call us today to schedule an inspection or start discussing safety needs.